An interview with Jelena Mirkov, Lead 3D Artist at SENAR
As our Lead 3D Artist, Jelena oversees all the 3D assets at the heart of our AR simulators. She is passionate about architecture and video games, and also practices sculpture. Her creativity is coupled with great rigor and precision, a combination that works wonders for modeling realistic simulators designed to train professionals. We asked her to tell us more about what goes into her job.
What is your creative process, and what are the steps involved in creating simulator assets from start to finish?
Before I begin 3D modeling, I often spend time researching and focusing on the main characteristics of the particular asset I am creating. I collect as many references as possible, from every angle, to make sure I don’t miss a single detail. Those may be photos, videos, or even quick sketches I put together to design a storyboard that will help me establish the guidelines I need to create the 3D object.
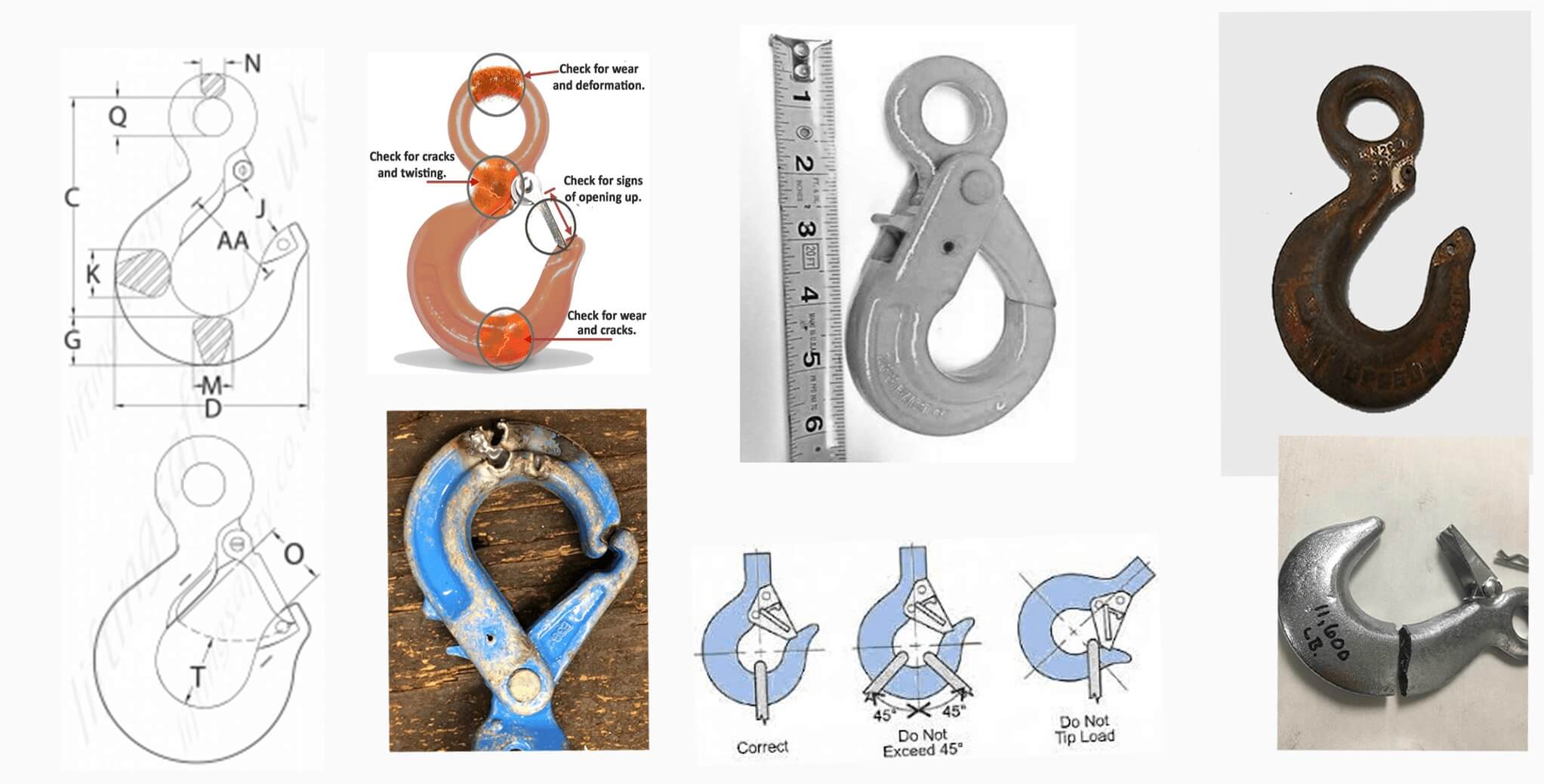
When creating 3D, I always start simple and work towards complexity. At the very beginning, I make a rough 3D object with its real-world sizes in the software I use the most – 3ds Max. This is very helpful for getting a sense of the general atmosphere & space between various objects in the scene. Once the ‘blocking’ stage is done, I add details to the objects – the bigger the object is, the more time I spend defining each of its parts. Since you can physically approach AR objects, this step is very important, especially when dealing with industrial complex objects. For those, I must ensure that each detail is geometrically correct. Also, for the sake of performance and to be able to display objects in AR with a high frame rate, it is very important to calculate every detail between or on the objects in focus, and determine which details are not relevant in a particular scene. Naturally, the ones in focus will be more defined and more attention will be given to them than to others in the scene. This is crucial to the fluidity of the AR experience.
The second parameter that defines an object is texturing. Once the modeling is done, I send objects to another software program I use called Substance Painter, where I add colors, paint surfaces and add more details such as reflections and refractions to make the model look more realistic. At this stage, I can play with physical light properties and fake small surfaces such as cracks, bumps and many other details that are not defined by geometry. Personally, this is my favorite part and I really enjoy using different art tools to completely transform a 3D object; like turning a brand new piece of metal into an old, worn and rusty piece of scrap metal. It is always fun to play with textures and add more details.
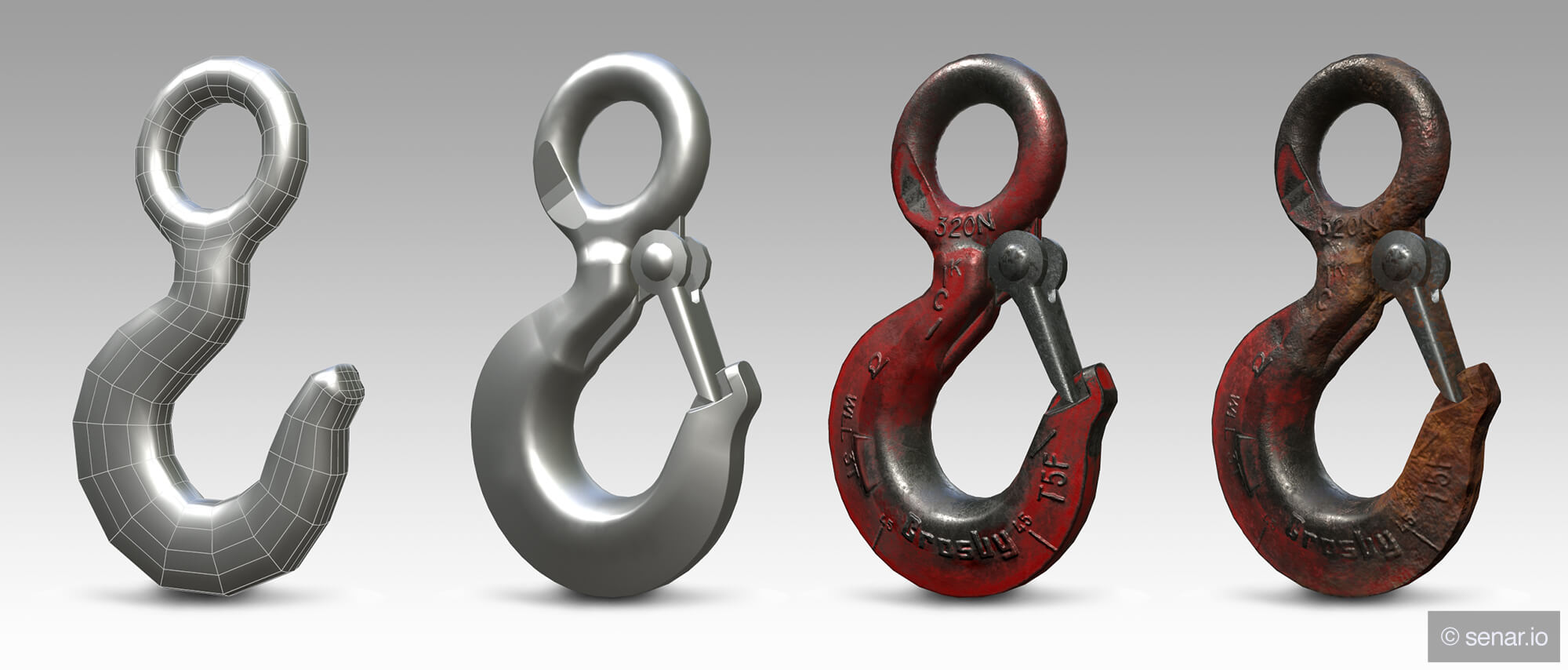
This is the very end of the process where I can add stickers such as manufacturer logos, safety signs, technical tags or other stamps to achieve maximum realism! I often redesign these elements myself for better readability. Our developers have even created a system that localizes their texts according to the user's language.
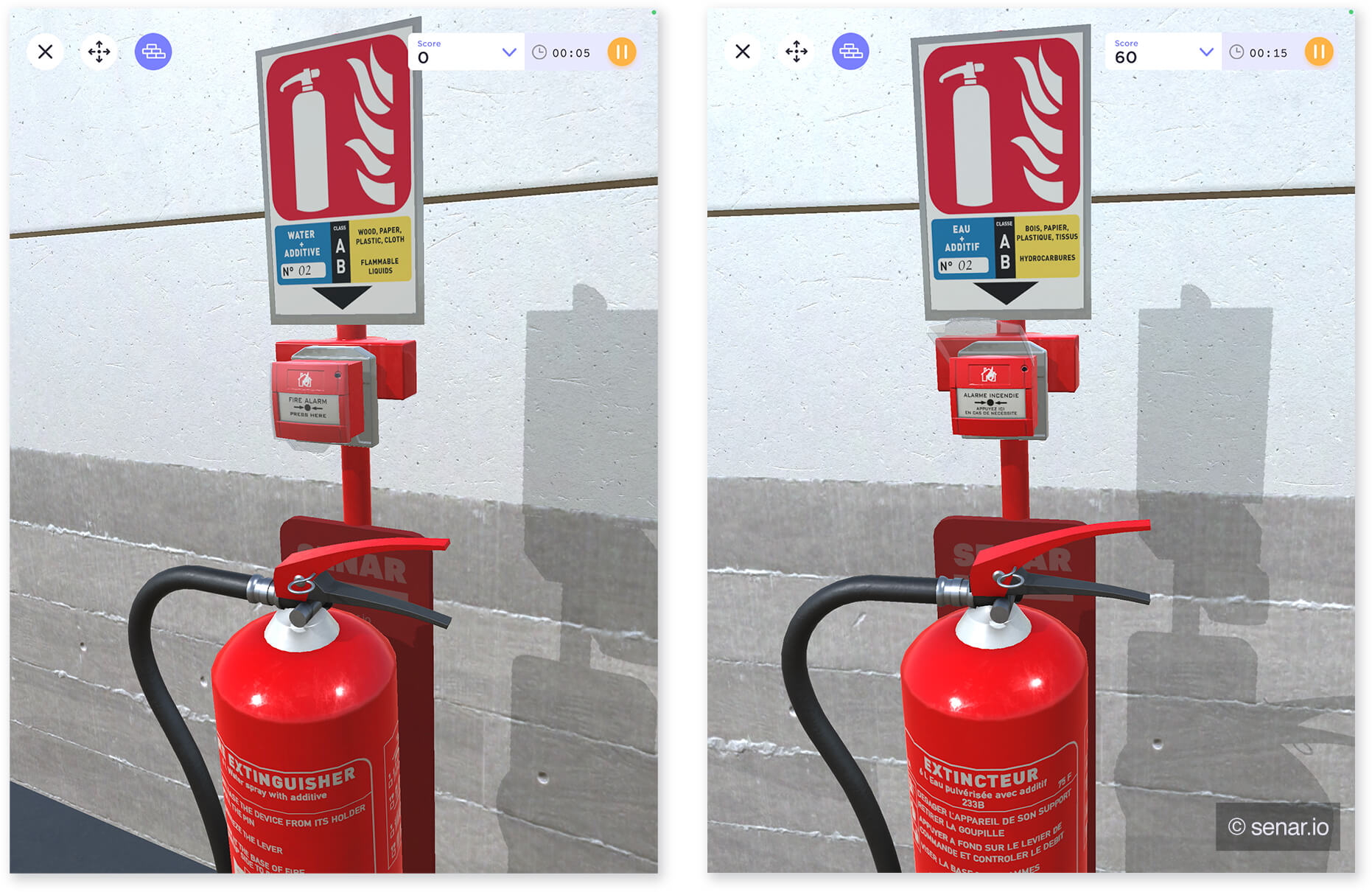
When the whole process is completed, I deliver both models and textures to our Unity coders where they proceed to render the scene and make it a fully interactive training simulator.
Your 3D assets are presented as life-size, and used for training purposes. How does that affect your process?
For an optimal AR experience, there are many factors and requirements I need to keep in mind when creating virtual assets. One is to ensure that assets displayed in life-size don’t lack any information or details in comparison to real-world ones. The number of polygons in geometry and the quality of the textures is one of the main factors of performance. AR doesn’t handle heavy assets very well because they overload the processor on mobile devices. Displaying life size objects must thus be optimized and well-organized in both the design and rendering stages. Unrealistic assets would be useless in training, especially for inspections. Pixel perfection is necessary for inspection sims where any discrepancy could wrongly be seen as a flaw on the object.
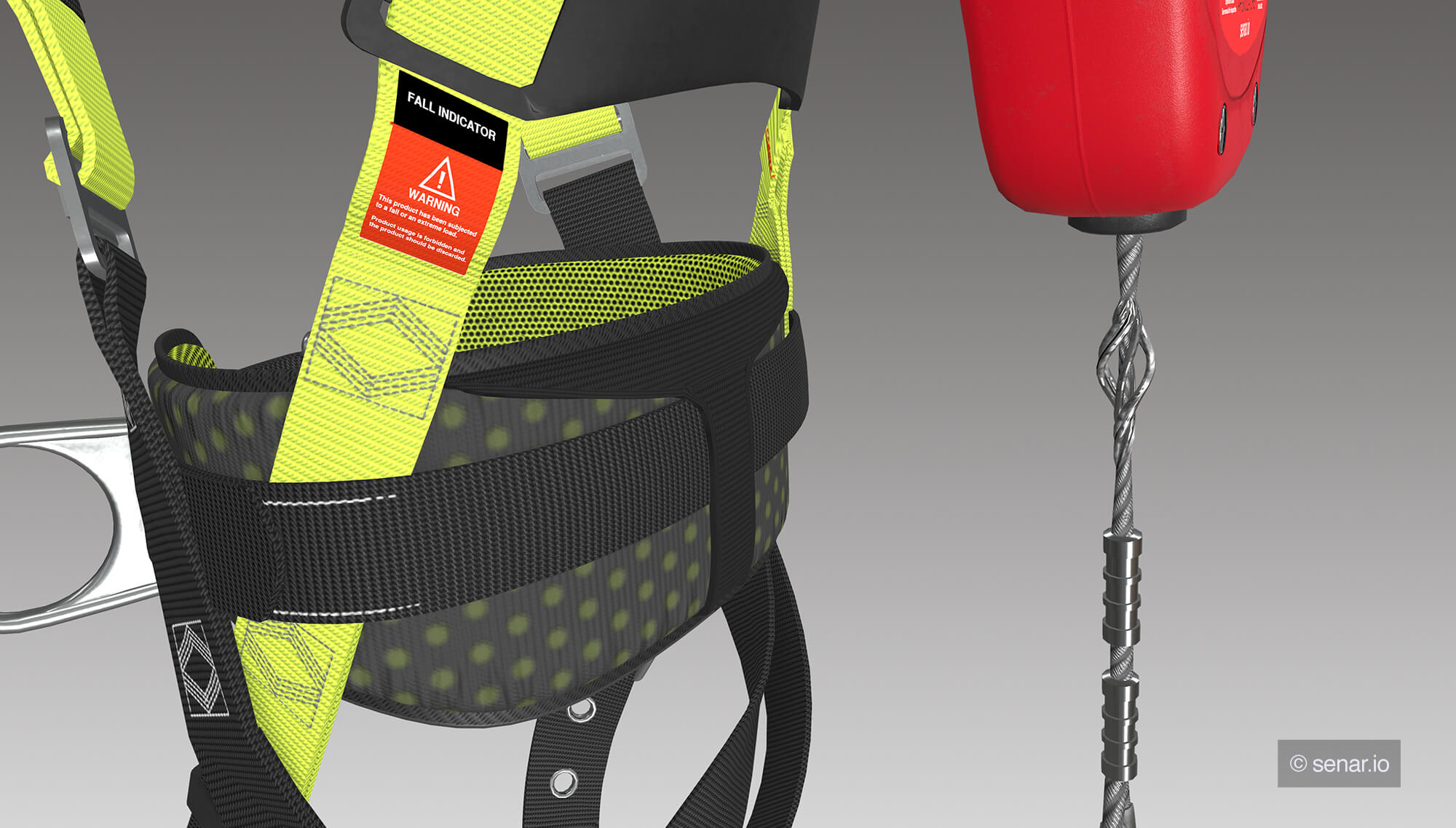
How did you start working in AR and decide to go from simple 3D to AR 3D?
I always wondered how my work would look in real life. I used to play a lot of video games when I was young, but never thought I would be able to interact with virtual objects. Coming face-to-face with my design for the first time in AR a few years ago, was a shocking moment for me! It has definitely changed the way I sense things and piqued my curiosity for learning new technologies. AR technology was familiar to me, but since I was working in the video game industry at the time, it seemed like something in the distant future! Luckily that future arrived quickly as I began digging deeper into AR and pursuing my passion for this new and challenging subject at SENAR. Working in the video game industry has given me a lot of experience that I still use in my work, but going from simple 3D to 3D AR has opened a new door for me where I have to take more care when creating assets.
Are there specific skills you had to develop to work with AR assets, and skills you would like to develop further in future?
Although I enjoy working on texturing the most, there are assets that require special care and are not easy to manipulate with the tools I use and have available. Since I can interact with my work in AR, I imagine one day I will be able to directly interact and define the assets in front of me. That would help me to better understand the reality of the object and it would also be fun to play with it.
I’m happy that I have great developers on the team, who are always there to help when I doubt myself, and who are committed to doing their best to make everything look even better in Unity. Unfortunately we’re often limited by technology and we must stick with what will work the best on users' devices. I hope one day technology will improve and we won’t have those limitations anymore. I really look forward to being able to add more physically based parameters to scenes, such as transparency, translucency and more defined lights and shadows that would make assets look even more realistic.
Which asset was the most fun to make, and which one are you the most proud of?
I would say the forklift. Even though it was one of the most complicated assets to do, I must admit I had a lot of fun working on it. I had a lot of challenges in making complex driving commands and flaws that would not be too easy to find during the forklift inspection. I also enjoyed texturing the metal parts covered with dust and rust and also adding small flaws to it.
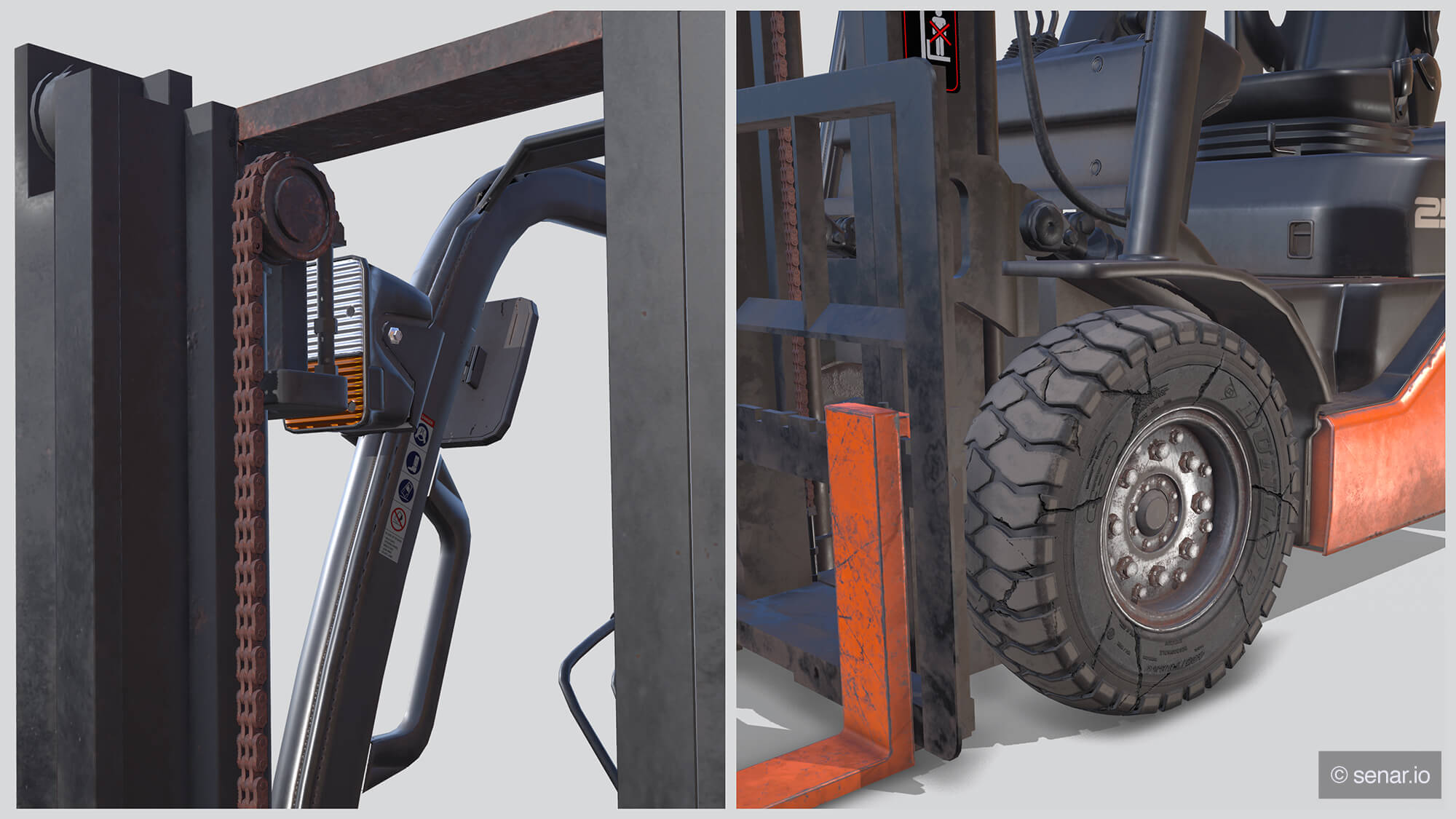
The funniest part came when I had to introduce the forklift in AR to my father, who is an expert in industrial vehicles. Being able to show him something that he sees every day at his job made me so proud! We had fun testing it and driving a forklift on my iPad along the street while neighbors gave us sideways glances. It did not take him long to understand the commands since they were already familiar to him.
He was finally able to understand what my job is about. 🙂
Which asset was the most frustrating?
Without hesitation, the electric enclosures! Modeling something simple that requires a lot of repetition, such as creating hundreds of cables, can be really frustrating. I have to make sure that each cable is connected properly, otherwise students might mistakenly think they’ve found a flaw during their risk analysis. Luckily, I haven’t actually had to design all cables one-by-one. My life-saving coders had the idea to develop a specific module in Unity. They saved me hours of a really tricky, repetitive task.
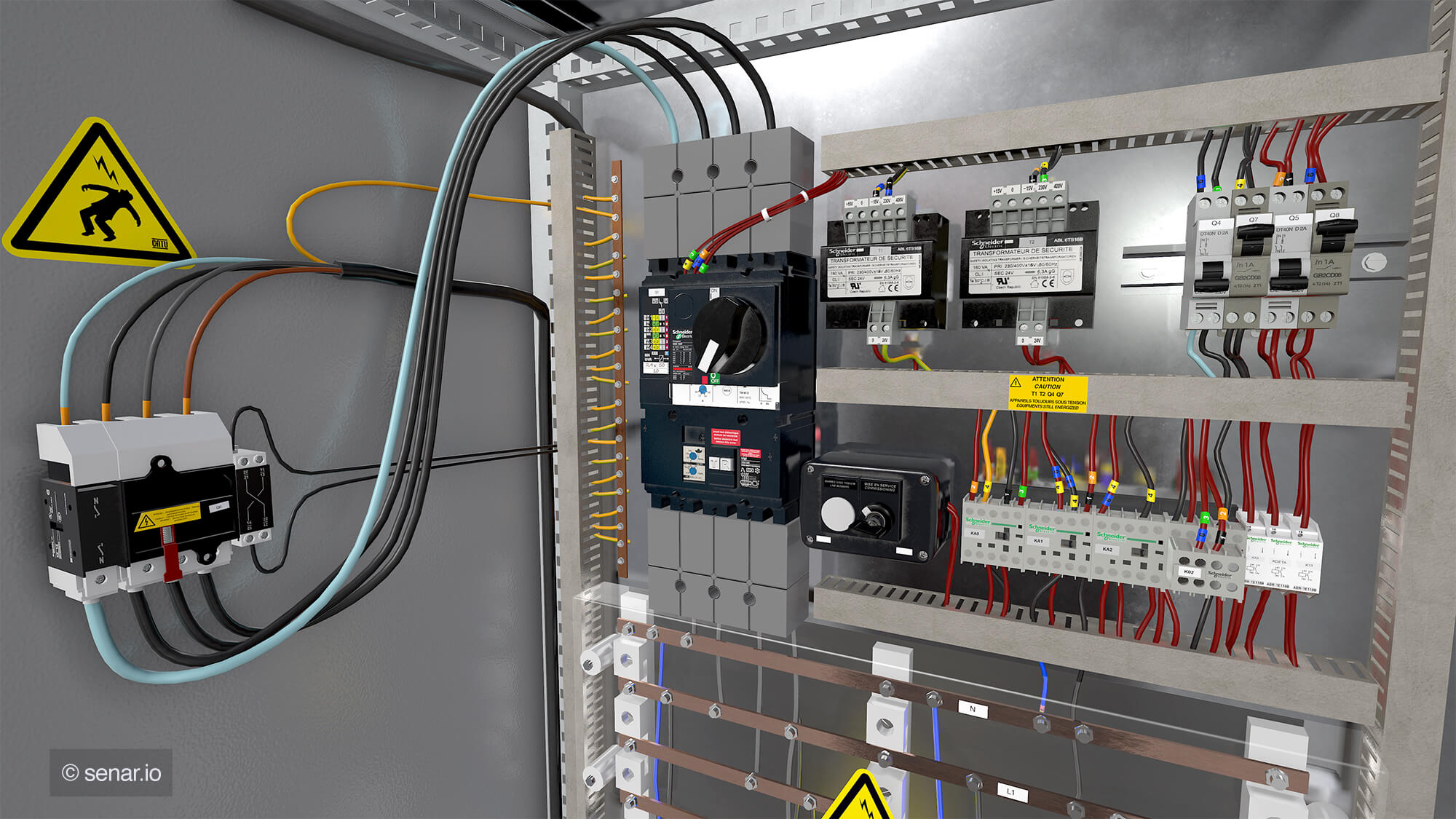
What's the best compliment you ever received from a SENAR client?
It was hard to appreciate the quality of my own work until clients, who are familiar with the real objects I’m modeling, complimented me. For example, the rigging instructor who works with ITI (International Training Institute) finds his job much easier using Augmented Reality. He believes that the SENAR training simulator helps to better engage students than more traditional learning methods. In one of his interviews, he explained:
I think the fact that the graphics are so good is what makes it so usable. If you’re looking at a shackle or a hook and you’re looking for a hairline crack or something like that, if the graphics weren’t very good it wouldn’t be useful.
This compliment made my day.